Partners
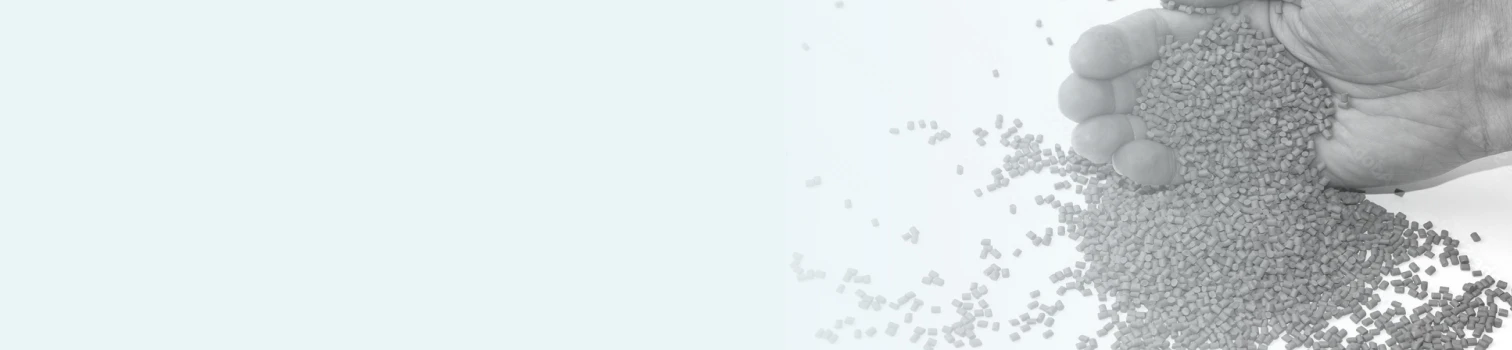
Together with our cooperation partners we offer a comprehensive service for the development, introduction and assistance for plastic recycling projects.
The consumption of plastic increases with prosperity in a region and so does the amount of plastic waste. For this reason, governments are currently developing various instruments to implement a Circular Economy. These include approaches such as reducing plastic production, reuse and strict regulation or banning landfills. Targeted policies address specific players in the market. These measures include, for example, the legal introduction of Extended Producer Responsibility (EPR) or binding requirements for the use of Recyclates in the manufacture of new plastic products.
The demand for (polymer) recyclates will therefore increase!
Generally plastic processors (own plastic waste) and recycling companies (mechanical processes with limitations) are interested in the CreaSolv® Process.
OEMs (Original Equipment Manufacturer) also search for solutions, how to separate post-consumer plastic waste from toxic impurities, because mechanical techniques fail and only the incineration is left or the waste ends up illegally in developing countries. All interested parties have in common that the required processing technology does normally not belong to their core competencies or equipment.
Because the entry barrier is high for such companies the available support offering covers the complete range from laboratory to the final production process and can be requested according to individual customer needs.
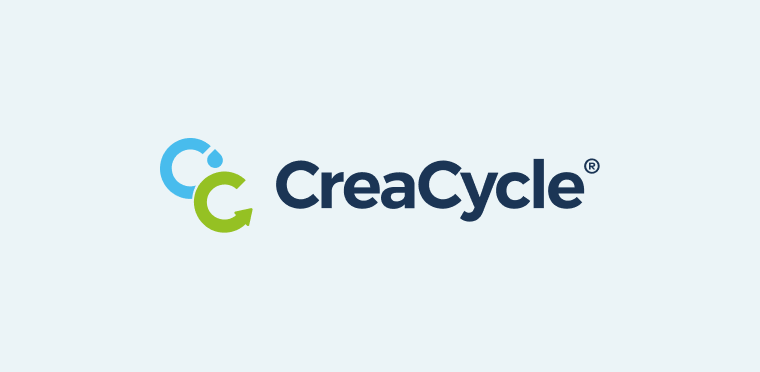
In 2002 the CreaCycle GmbH was founded as Start-up and offers special CreaSolv® Formulations for dissolving and recycling of plastics, designed for the CreaSolv® Process
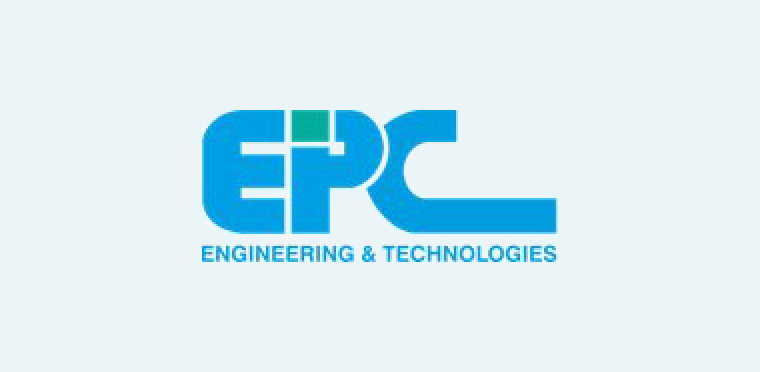
EPC Engineering & Technologies offers comprehensive competency in chemical plant engineering (polymerization), that reaches from conceptual engineering, planning and project execution to commissioning and final plant operation.
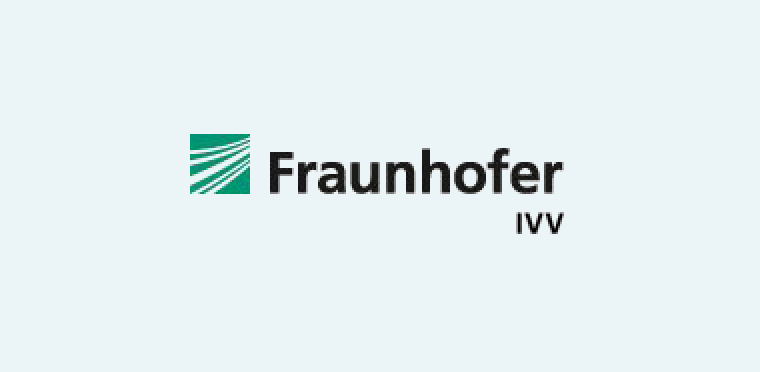
The Fraunhofer Institut IVV is specialized in process development for the patented CreaSolv® Process, a solvent-based recycling process.
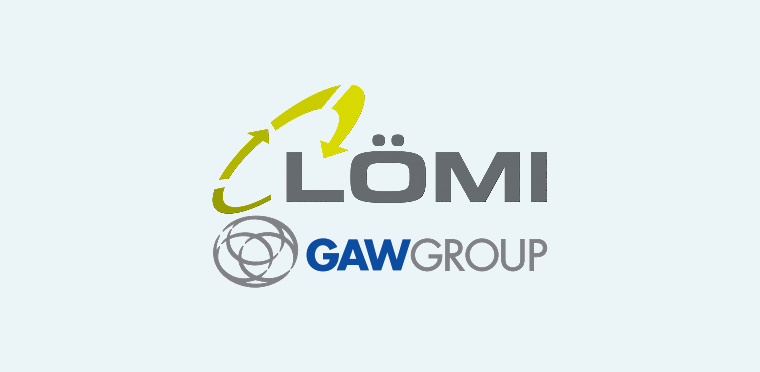
LÖMI GmbH has been developing high-quality and innovative process engineering systems since 1991, especially for handling solvents.